Les savoirs utiles pendant le cursus de CAP
Tout au long de votre formation, vous allez découvrir de nombreux savoirs vous aidant dans l'acquisition des compétences pour devenir "Chaudronnier Industriel".
A travers ces différentes parties, vous allez obtenir les informations nécessaires pour votre cursus CAP RICS.
Retrouver au format PDF, la totalité du "Livre Numérique" édition du 13 mars 2023 : Savoirs _en_RICS_2023-03-13.pdf
S1 : La communication professionnelle⚓
.
S11 - La communication professionnelle⚓
A tous les niveau
S11-1. L'ouvrage ensemble fonctionnel⚓
.
S11-2. Spécifications normatives et réglementaires⚓
.
S11-3. Cotation⚓
La cotation est très importante sur un dessin. Pour être comprise de tous, il faut respecter plusieurs point :
l'écriture ; elle doit être normalisée
les règles de cotation : 2 lignes de rappels, une ligne de cote avec une double flèche. La cote sera toujours inscrite SUR le trait de cotation.
S11-4. Documents de fabrication⚓
Document de fabrication
.Les documents de fabrication permettent de classer les informations mais aussi de préparer le travail à faire :
Gamme de fabrication⚓
LA gamme de fabrication est la « recette » pour réaliser la pièce du début à la fin. Ce document indique les machines et les réglages nécessaires mais aussi, les outils de contrôle qu'il faut pour vérifier les cotes.
Voilà un exemple de gamme :
Graphe de montage (ou râteau)⚓
Le râteau de montage permet d'assembler l'ensemble de tôlerie dans l'ordre choisi par le dessinateur ou le responsable de l'atelier.
Le respect des cotes mais aussi, l'accessibilité est très importante.
Planning de phases d'un ouvrage⚓
Fiche débit⚓
Les matériaux nécessaires
Il est toujours utile de calculer le nombre de barres ou de feuilles de métal avant de commencer la fabrication
Mise en tôle / Barre économique⚓
L'imbrication économique ....
Afin de pouvoir fabriquer les ensembles ou pièces de façon la plus économique, il est nécessaire de prévoir les quantités de matériaux minimale.
Les matériaux peuvent être soit :
- Des formats de tôles (tôles perforées, tôles planes, ...)
- Des profilés (barre de tubes, poutre type IPN, des plats, ...)
Les formats standards
D'une manière générale, on s'approvisionne chez les fournisseurs de barres et tôle de formats standards :
Les barres ont une longueur de 6 m (ou quelquefois 12 m)
Les tôles sont disponibles dans les formats suivants :
1000 x 2000
1250 x 2500
1500 x 3000
Il est également possible d'avoir des formats hors standard pour une commande spéciale, mais dans ce cas, les délais de fabrication peuvent être allongés.
Les catalogues
Pour connaître le poids des matériaux, on utilise des catalogues qui nous indiquent les poids des matériaux commandés :
- A partir de la « masse linéaire » pour les tubes , profilés, et laminés
- Le poids de la tôle pour les surfaces
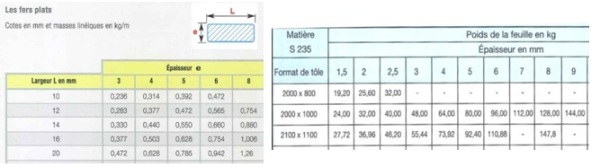
I - Les longueurs de barres⚓
Les produits laminés
A partir de la longueur de la pièce désirée, On réalise l'opération suivante :
Par exemple, nous avons besoin de débiter 10 barres de tubes ø33.7x2, d'une longueur Unitaire de 1300 mm.
De combien de barres de 6 m ai-je besoin ?
Réaliser l'imbrication à l'aide de la fiche ci après
Exemple :
Je commence à identifier la longueur de la pièce : 1300 mm
Je sais qu'il faut des barres de longueur 6000 mm
Je calcul le nombre de pièces dans une barre : 6000 / 1300 = 4.6 soit 4 pièces dans une barre
2. Je calcul combien de barre j'ai besoin : 10 / 4 = 2.5 soit 3 barres
II - Les produits plat⚓
Les plaques et tôles
A partir d'un plan de pièce obtenu : il me suffit de diviser la longueur de la tôle par la longueur de la pièce, puis ensuite de diviser la largeur de la tôle par la largeur de la pièce.
Je schématise le format de tôle de 1000 x 2000. Dimensions du flanc de pièce : 150 x 320.
Réaliser l'imbrication à l'aide de la fiche ci après
III - Fiche Mémo : L'imbrication⚓
Retrouver ici la fiche mémo pour calculer rapidement et efficacement les imbrications dans une barre ou une tôle
Fichier à utiliser ici :
Le cours :
S11-5. Règles et normes de représentation des ouvrages⚓
Vue américaine ou européenne ?
Pour réaliser un plan il faut réaliser le plan de détail suivant la norme européenne.
Pour mettre en application cela, il faut placer les vues judicieusement. :
la vue de face est au centre, elle donne le plus d'indications
la vue de droite est placée à gauche,
la vue de gauche est placée à droite...
et ainsi de suite.
S11-6. Les solutions constructives⚓
.
S11-7. Règles de représentation et de symbolisation des assemblages soudés et filetés⚓
.
S12 – La représentation d'un ouvrage⚓
.
S12-1 Règles et normes de représentation des ensembles chaudronnés⚓
Représentation d'une pièce, ou d'un ensemble.
La communication technique est primordiale. C'est grâce à elle que l'entreprise dialogue avec ses clients et ses fournisseurs.
Au sein de l'entreprise, la représentation d'une pièce permet de valider les caractéristiques entre les différents services : commercial, bureau d'études, service achats et atelier de fabrication.
Une erreur de représentation, de cote ou d'annotation risque de compromettre la réussite du projet.
Le risque est également financier : reprise de la pièce, pénalité de retard....
Présentation de l'ensemble chaudronné
L'ensemble présenté ci après comprend un réservoir avec des piquages tubulaires sur la partie supérieure et latérale.
Le réservoir est positionné sur 3 pieds en fer UPN avec des platines à fixer au sol.
Définition : Le plan d'ensemble ....
Le plan d'ensemble présente l'objet, l'ensemble des pièces à réaliser, ou à assembler.
On trouve, sur chaque plan d'ensemble, des éléments permanents : la nomenclature, et le cartouche.
Qu'est ce qu'une nomenclature ?
La nomenclature est la liste des pièces ou sous-ensemble présent sur l'ensemble lui même. On peut voir dans une nomenclature :
- un repère qui permet d'identifier la pièce sur le plan
- une quantité dénombrant les pièces identiques présents sur le sous ensemble / ou l'ensemble
- une désignation
- la matière de l'élément
- une observation pour donner des indications complémentaires (référence à un plan, une norme, .... )
Qu'est ce qu'un cartouche ?
Le cartouche permet d'identifier le plan. On y voir des informations permettant de connaître :
- le titre du plan indiquant le nom de l'ensemble et le nom du plan
- le dessinateur
- la date de réalisation
- un indice de révision
- l'échelle du plan
- le nom de l'établissement
- la référence du plan permettant un archivage
La lecture d'un plan, comment ça marche
Pour représenter le volume d'une pièce ou un ensemble sur une feuille, il est nécessaire de procéder à la représentation des vues "à plat", c'est à dire, en 2 D.
Afin de pouvoir visualiser la pièce dans son ensemble, plusieurs vues peuvent être nécessaire comme le montre l'image suivante.
On prendra soin d'aligner les différentes vues pour assurer une concordance des vues entres -elles.
Définition : Plan d'ensemble, de sous ensemble et d'éléments.
Le plan d'ensemble permet de représenter une installation, ou un ensemble mécano-soudé dans son ensemble.
Les cotes d'encombrements sont présentes et permettent de prendre en compte l'environnement de l'ensemble.
Par exemple, pour un réservoir, les cotes de niveau sont présentent pour permettent de le raccordement de l'appareil.
On voit apparaître une nomenclature indiquant les sous ensembles, pièces seule, ou éléments de visserie présentes sur l'ensemble.
La vue principale est la représentation de l'ensemble lors de son fonctionnement. En général, il s'agit de la vue de face
Le plan de sous ensemble est la représentation d'une partie de l'ensemble présent sur l'installation.
Un Sous ensemble est constitué de 2 pièces minimum, assemblées de manière définitive par un cordon de soudage, par collage, ou par déformation de matière (emboutissage, agrafage... )
Sur le plan d'un sous ensemble, on voit apparaître une nomenclature des pièces soudées constituantes du sous ensemble.
Le plan de détail ou de fabrication donne toutes les indications nécessaires à sa fabrication dans un atelier : matière, tolérance de fabrication,
Définition : Schéma de principe d'une installation d'un sous ensemble.
Le schéma de principe de l'installation permet de comprendre rapidement le fonctionnement de celui ci, sans pour autant avoir toutes les informations indispensables à la réalisation (cotation de soudure, dimensions précises de fabrication, .. )
Par rapport au plan présenté ci dessous, le schéma permet cependant d'avoir les informations principales :
- dimensions entrée et sortie de fluides,
- hauteur de raccordement
- dimensions globales de l'ensemble.
Représentez un schéma de principe du réservoir présenté ci dessus.
Définition : Représentation isométrique.
Nous distinguerons 2 types de représentations ISOMÉTRIQUE :
- la représentation d'une pièce dans l'espace,
- la représentation d'une portion de tuyauterie
- la représentation d'une pièce dans l'espace :
Pour la représentation d'une pièce, il y a 2 types de représentations :
- La perspective cavalière (les fuyantes sont à 45°)
- la perspective isométrique (seulement 1 axe est vertical, les 2 autres sont incliné à 45 °)
La représentation d'une portion de tuyauterie permet de modéliser, sur une seule planche de dessin, les propriétés de la portion de tuyauterie. Elle est très utilisées dans le domaine de la tuyauterie industrielle.
Croquis à main levée.
Le croquis à main levée permet de donner rapidement une idée en vue de la réalisation d'un projet.
On peut voir apparaître sur le croquis les côtes nécessaires à la conception finale de la pièce.
Sur le croquis, il est important d'y faire apparaître l'environnement de la pièce (ce qui l'entoure, les éléments à prendre en compte à proximité de l'élément à définir)
Exemple : Exemple d'analyse d'un plan d'ensemble
Ci après, un exercice à réaliser pour l'étude et le repérage des pièces sur un plan d'ensemble. Le coloriage est très important et facilité la lecture du plan.
Dans la deuxième partie, vous devrez réaliser un plan de détail de 2 pièces (une pièce à plat et une pièce de tôlerie pliée)
S12-2. La modélisation numérique en 3D⚓
Le logiciel SOLIDWORKS.
Ce modeleur présent dans l'industrie permet de concevoir des pièces de toutes formes possible. Pour des pièces de tôlerie, le logiciel nous permettra de préparer les pièces à plat pour une fabrication à l'aide d'une Machine Outil à Commande Numérique de type centrale Laser, Plasma ou poinçonnage.
Évidement, chaque logiciel permet également une mise en plan, nécessaire pour une fabrication dans l'atelier.
S12-3. Exploitation d'un modeleur volumique⚓
.
S2 : Les matériaux et produits d'apports⚓
A chaque application son matériaux ...
Les nuances d'aciers sont multiples :
l'acier à peindre pour de multiples application (menuiserie métallique, ... )
les inox pour l'industrie pharmaceutiques ou agroalimentaire
les alliages pour l'aéronautique
les fontes pour des applications spéciales (radiateur bâti machine)
...
Les applications sont nombreuses, tout comme les types d'acier.
S21 – Les matériaux de base⚓
Matière première et métal d'apport... Quelle est la différence ?
Le chaudronnier utilise des matières premières : des tôles, des tubes, des profilés. Pour assembler ses pièces, il a besoin d'utiliser des procédés de soudage comme les MAG, l'électrode enrobée.
Il existe de nombreuses nuances d'acier mais également de métal d'apport.
Dans un premier temps, vous découvrirez comment est fabriquée la matière première, puis dans un deuxième temps, nous spécifications les termes des produits élaborés et pour finir, vous verrons comment choisir le métal d'apport.
S21-1. Caractéristiques des matériaux⚓
Les procédés d'obtention⚓
Le minerais de fer ... mais pas seulement.
Pour produire de l'acier, il existe plusieurs procédés :
- à partir du minerai de fer. Le problème est la disponibilité des ressources naturelles qui diminuent.
- à partir des aciers recyclés que l'on trouve dans les déchetteries ou chez les ferrailleurs.
Complément : Émission "C'est pas sorcier"
La célèbre émission "C'est pas sorcier" vous explique l'obtention des aciers. C'est une procédé issue de l'industrie Métallurgique.
Rendez vous sur le lien suivant pour la diffusion sur le site youtube.
Désignation normalisée (notions, familles de matériaux) et formes commerciales.⚓
Un nom, une forme
Pour pouvoir fabriquer des ensembles chaudronnés, le concepteur doit puiser dans un catalogue de formes génériques, avec des nuances d'acier qui sont connues. Nous allons découvrir ces 2 points particuliers ci après.
Définition : Désignation normalisée
Entre les Aciers de construction ou aciers pour les appareils sous pression, chaque acier a sa désignation normalisée :
les aciers de construction
les aciers pour les appareil à pression
les tubes pour canalisation
Définition : Formes commerciales
Il existe de nombreuses formes commerciales pour acheter des produits métalliques :
les plaques d'acier
les tôles
les tubes ronds
les profils creux (carré ou rectangulaires)
les laminés (plat, rond, carré) ou profils spécifiques : UPN, IPN, HEB,...
les étirés (plat ou rond)
Pour chaque formes, il existent plusieurs nuances. A préciser pour chaque affaire.
Vous pouvez retrouver un catalogue complet des produits laminés ici
Caractéristiques mécaniques :⚓
- Résistance.
- Dureté.
- Résilience.
- Élasticité.
Caractéristiques physiques⚓
- Plasticité.
- Conductibilité.
- Soudabilité.
Caractéristiques chimiques⚓
- Corrosion.
S22 – Les produits d'apports⚓
.
S22-1. Les métaux d'apports⚓
.
S22-2. Les gaz et les flux⚓
Il existe différent gaz :
Pour le soudage électrique (MIG/ MAG / TIG) : des mélange de différents gaz : Argon, CO2,
Pour le soudage oxyacétylénique : Oxygène, Acétylène
Pour les procédé de découpage (plasma ou laser) : Oxygène, Azote, Argon
Les gaz sont comprimés dans des bouteilles qu'il faut manipuler délicatement.
S23 – Les éléments de construction⚓
S3 : Les procédés⚓
Les procédés dans un atelier de chaudronnerie.
Débit, usinage, conformation ou soudage, tous les procédés sont récapitulés ici : Les machines Outils dans l'atelier de Chaudronnerie Industrielle
Vous pourrez ensuite tester vos connaissances sur les machines outils de l'atelier et les phases de fabrication avec une application ludique : cliquez ici
S31 – Les procédés de fabrication⚓
S32 – Les procédés de conformation⚓
.
S32-1. Techniques de déformation plastique⚓
Déformation de la matière...
Pliage⚓
Le pliage....
Procédé de fabrication présent dans tous les ateliers, les techniques de pliage sont nombreuses, les règles à respecter
1 - LES DIFFÉRENTES MACHINES OUTILS⚓
La presse plieuse
La presse plieuse à commande numérique
La presse plieuse à commande numérique permet la fabrication en série de pièces de tôlerie.
Avec une programmation possible via un pupitre de programmation, les étapes de fabrication sont stockées dans l'ordinateur de bord.
2 - LES FORMULES A CONNAÎTRE PAR CŒUR⚓
Rappel : La valeur du Vé et le Rayon intérieur
Pour des calculs standard et la modélisation des pièces, il faut prendre en compte le calcul suivant :
Vé = 8 x ép
Ri = Vé / 6
La longueur développée
Pour calculer les longueurs développées des pièces, il y a 3 méthodes envisageables :
- la méthode des cotes intérieures
- la méthode des cotes extérieures, dite du ΔL (perte au pli)
- le calcul en fibre neutre
MÉTHODE : Les cotes intérieures⚓
Pour une pièce ne possédant qu'une valeurs de pliage à 90°, la méthode des cotes intérieures est la plus simple. En effet, il suffit d'additionner toutes les cotes "en intérieur" des plis pour avoir la longueur développée. Attention cependant au choix du Vé.
Méthode : Formule
LDint = Σ cotes intérieures
Attention : Uniquement dans certains cas...
Dans quel cas utiliser le calcul de la LDint ?
Le calcul n'est possible que dans le cas où :
- la valeur du Vé utilisé est égale à 8 fois l'épaisseur : Vé = 8 x ép
- la valeur des angles de pliage sont de 90°
Dans les autres cas, cette méthode de calcul n'est pas possible.
Complément : Rendez vous sur internet pour une explication
MÉTHODE : Les cotes extérieures dite du ΔL (perte au pli)⚓
Pour une pièce de tôlerie possédant plusieurs valeurs de pliage, la méthode des cotes extérieures est utilisée. En effet, après avoir validé certains paramètres, il suffit d'additionner toutes les cotes "en extérieur" des plis puis additionner la somme de "pertes aux plis" pour avoir la longueur développée.
Méthode : Formule pour calculer la Longueur développée
LDext = Σ cotes extérieures + Σ Δl
Vous remarquez l'addition de la somme des pertes au pli. En effet, dans la plupart des cas, la perte au pli est négative (voir l'exemple plus bas) mais parfois,la perte au plis est "positive"
Exemple d'une pièce de tôlerie
Étudions la pièce de tôlerie suivante :
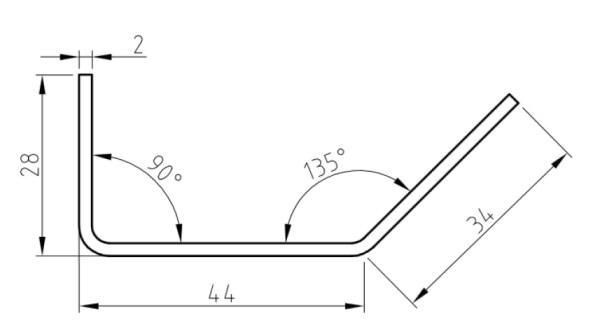
Dans la majeur partie des cas, la méthode de calcul avec les cotes extérieure est à privilégier. La fabrication standard (avec la méthode des cotes intérieures) n'est pas possible. En effet, plusieurs paramètres sont à vérifier avant le calcul de la longueur développée :
- la valeur du Vé disponible à l'atelier : l'outil nécessaire existe t-il ?
- les valeurs d'angle : quels sont les angles présents sur la pièce ?
- le bord mini de la pièce : le choix du Vé est-il possible avec la conception de la pièce ?
- Le Rayon intérieur : y a t-il une obligation sur le plan qui obligerait de choisir l'outil par rapport au Ri ?
Une fois l'épaisseur et le Vé choisi, on pourra ainsi déterminer la "Perte au pli" pour chacun des angles de pliage de la pièce.
On retient, dans notre cas :
- Pour un pli à 90° : Δl90° = -4
- pour un pli à 135 ° : Δl135° = -1.2
Pour calculer la longueur développée, il faut donc procéder de la façon suivante :
LDext = ( Σ cotes extérieures ) + ( Σ Δl de tous les plis), ce qui donne :
LDext = (28 + 44 + 34) + ( Δl90° + Δl135° ) =
LDext = ( 106 ) + ( -4 + -1.2)
LDext = 100.8 mm
Méthode : Rappel, pour un angle différent de celui du tableau
Comment trouver une perte au pli pour un angle différent de ceux inscrits dans le tableau ? Par exemple, 40°, avec une tôle de 3 mm, Vé de 20 mm
Pour calculer précisément un angle qui n'apparaît pas dans le tableau des pertes au pli, il faut travailler méthodiquement :
Il faut trouver la proportionnalité entre 2 angles (Prenons 30° et 45°)
-0.2 mm | -1.3 mm | ? | -2.5 mm | |||
15° | 30° | 40 ° | 45° |
Pour définir la perte au pli pour l'angle à 40°, je calcul la différence entre les 2 valeurs du tableau :
Soit : 2.5 - 1.3 = -1.2
1.2 pour 15°, ce qui donne (1.2/3) = 0.4 mm pour 5°.
Je les ajoute à la valeur de -2.5, ce qui donne : -2.5 + 0.4 = -2.1.
Donc Δl40° = -2.1 mm
Complément : Utiliser l'abaque de pliage
Pour les calculs de Longueur développée avec la méthode du Delta L (ΔL), vous pouvez utiliser le fichier suivant :
Complément : Vidéo pour la méthode de calcul
Vous pouvez retrouver une vidéo de l'AFPA pour le calcul de la longueur développée d'une tôle
Durée : de 0'00 à 2'32 : Calcul de la LD
A partir de 2'33 : méthode pour le calcul des mises en butée.
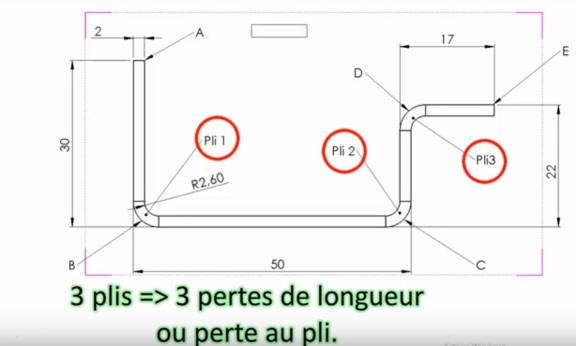
Autre présentation sur la méthode de calcul par la perte au pli
Méthode : Calcul d'une cote machine⚓
Positionner la butée machine
Dans certains cas, quand la MOCN ne dispose pas d'ordinateur de calcul de la Longueur Développée , il faut calculer la mise en butée pour chacun des plis
Pour ce faire, il faut procéder de la façon suivante :
Méthode : Formule de calcul : Cote Machine
cm = Σ cotes extérieures + Σ Δl(entre le pli et la mise en butée) + Δlpli / 2
Exemple de calcul d'une cote machine⚓
Exemple d'une pièce de tôlerie
Première possibilité :
Reprenons l'exemple ci dessus, avec les plis déjà répertoriés :
Δl90° = -4 et Δl135° = -1.2
1er pli : Calcul de la mise en butée pour réaliser le pli à 90° en cote directe :
cm1 = Σ cotes extérieures + Σ Δl(entre le pli et la mise en butée) + Δlpli / 2
cm1 = 28 + 0 + (-4 / 2)
cm1 = 26
2ème pli : Calcul de la mise en butée pour réaliser le pli à 135° en cote directe :
cm2 = Σ cotes extérieures + Σ Δl(entre le pli et la mise en butée) + Δlpli / 2
cm2 = 34 + 0 + (-1,2 / 2)
cm2 = 33,6
Deuxième possibilité pour en modifiant l'ordre de pliage :
Il est possible de modifier la mise en butée et la cote machine.
Reprenons l'exemple ci dessus, avec les plis déjà répertoriés :
Δl90° = -4 et Δl135° = -1.2
1er pli : Calcul de la mise en butée pour réaliser le pli à 90° en se mettant en cote indirecte :
cm1 = Σ cotes extérieures + Σ Δl(entre le pli et la mise en butée) + Δlpli / 2
cm1 = (34 + 44) + (-1,2) + (-4 / 2)
cm1 = (78 - 1,2) + (-2) = 74,8
2ème pli : Calcul de la mise en butée pour réaliser le pli à 135° en cote directe :
cm2 = Σ cotes extérieures + Σ Δl(entre le pli et la mise en butée) + Δlpli / 2
cm2 = 34 + 0 + (-1,2 / 2)
cm2 = 33,6
MÉTHODE : Calcul en Fibre Neutre⚓
Ligne droite et portions de cercle...
Cette méthode est utile dans le cas de fabrication avec une plieuse universelle ou à sommier.
En effet, avec le montage de certains outils, le rayon intérieur peut être maîtrisé et totalement différent d'un outil de presse plieuse...
Dans certains cas, il est même possible de réaliser la pièce par plis successifs.
Pour développer une tôle, il faut faire l'addition des portions droites et courbes.
dessin à venir...
Cours à distribuer⚓
Calculs des longueurs développées
Retrouver ci après le cours récapitulatif des 3 méthodes.
Calculs des Cotes Machines
Pour positionner la butée arrière sur la Commande numérique, il faut calculer la cote de Mise en butée.
Voyez sur le cours suivant la formule à retenir.
EXERCICES⚓
Recueil d'exercices
A travers plusieurs exercices, préparez vous à plier les pièce sur Presse plieuse Amada ..
Exercice sur le porte manteaux
Exercice sur le Range Feuille
Roulage⚓
Le roulage
Cette opération permet la réalisation de pièce cylindrique , en totalité ou en partie.
Les pièces roulées sont nombreuses tout autour de nous :
- citerne de stockage de carburant
- cuve de préparation pour le domaine agroalimentaire (pâte à tartiner, sauce ... )
- chaudière ou appareil sous pression
- fuselage d'avion,...
- pièce de tôlerie en général
toutes ces réalisation nécessitent la réalisation d'une opération de roulage
La technologie des machines outils⚓
Des machines différentes, pour une même opération de fabrication
Les machines outils sont de deux types, il y a une machine de type planeur, ou de type pyramidale.
Le fonctionnement se fait soit de manière manuelle, soit électrique.
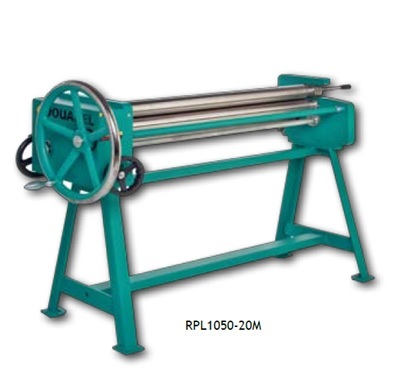
Ici, la virole est entraînée à l'aide du volant de manœuvre.
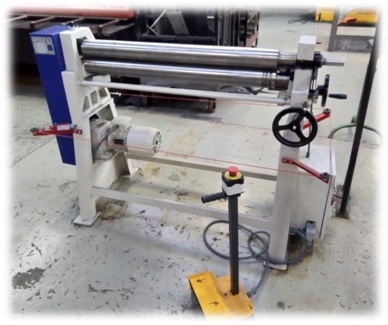
Sur cette machine, c'est un moteur qui entraîne la tôle. Le rouleau cintreur se déplace verticalement. il est manœuvré à la main sur ce modèle.
Les formules à retenir⚓
Calcul de la LD
Pour calculer la longueur développée d'une virole, il faut respecter 2 étapes :
déterminer le diamètre à la fibre neutre ou diamètre moyen (øFN)
calculer la longueur développée (LDfn)
Représenter le flanc capable en indiquant les 3 cotes nécessaires à l'opération de débit
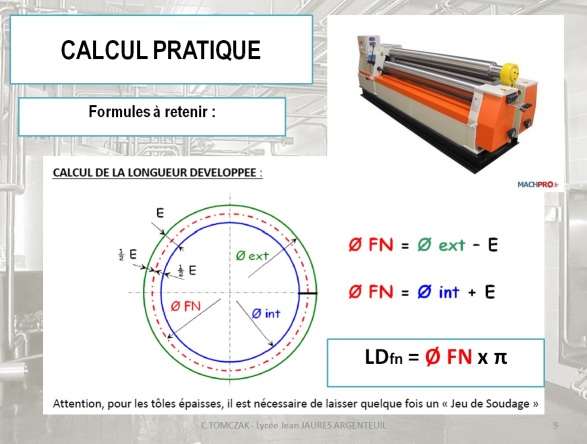
Exemple : La virole ... déjà vue !
Pour imaginer ce qu'est une virole, il suffit de regarder une bouteille d'eau cylindrique. L'étiquette vient s'enrouler sur le tour de la bouteille.
Si vous coupez l'étiquette, vous obtenez alors un rectangle !
Résultat
Vous cherchez à obtenir le flanc capable de la virole, c'est à dire, avant roulage. Il faut pour cela indiquer les 3 cotes du flanc capable :
la Longueur développée à la fibre neutre : LDfn
la longueur de la virole : L
l'épaisseur : e
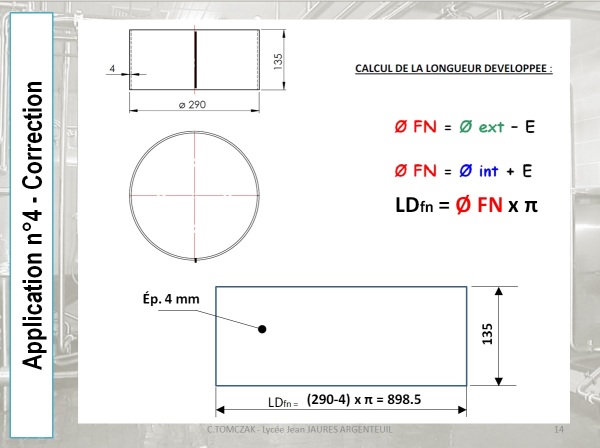
Calcul de virole n°1
Question⚓
Le Cintrage⚓
Utilisé pour la tôle ou les profilés.
Le cintrage est utilisé pour réaliser des pièces cintrée à partir de barre de métal : cornière, tube carré ou rectangulaire, ....
Mais aussi, une partie de tôle cintrée
Formule⚓
La formule de base
Pour calculer la longueur développée est : P= pi x 2 R
Mais il peut y avoir aussi une portion de forme cylindrique, dans ce cas, la formule est P = ((pi x 2 x R)/ 360) x angle
Les machines de cintrage utilisée.
Pour former la matière, plusieurs possibilité :
la rouleuse
la cintreuse de profilés
S33 – Les procédés de soudage⚓
.
S33-1. Le soudage par fusion⚓
.
Type de courant délivré pour les générateurs de soudage⚓
Réseau Electrique
L’assemblage, lors des opérations de soudage électrique, est réalisé par un poste à souder connecté au réseau électrique.
Pour rappel, le réseau électrique français délivre, chez les particulier et les entreprises un courant alternatif monophasé dont la tension est de 220 V, et la fréquence de 50Hz.
Pour les entreprises, gourmande en électricité et dont les machines-outils nécessite une grande quantité d’énergie , le courant distribué peut être de 380 à 400 V. Il s’agit alors d’un réseau triphasé. Mais la fréquence du courant délivré reste 50Hz
Les procédés de soudages sont nombreux et les caractéristiques de fonctionnement, également.
Dans tous les poste à souder, on peut trouver un transformateur ou une carte électronique permettant de générer un courant continu ou de modifier les paramètres du courant alternatif.
Principe de l’arc électrique : notions de base⚓
Un arc électrique se forme lorsque le différentiel de tension avoisine 0V. En effet, il suffit de mettre en court-circuit les pôles d’un circuit électrique pour voir se former l’arc électrique.
Mise en œuvre et techniques opératoires en fonction des procédés.⚓
Pour Chaque situation, le procédé utilisé sera adapté. Dans de nombreux cas, il existe aussi bien le procédé manuel et automatisé.
|
|
TIG manuel | TIG automatisé |
Dans le domaine de la ventilation ou de la carrosserie, le procédé SERP est utilisé mais pour augmenter la productivité, le procédé peut être automatisé.
SERP manuel | Robot de soudage carrosserie |
Par exemple, pour une soudure sur chantier, on pourra privilégier les petites installations pour déplacer facilement le poste à souder.
Arc électrode enrobé sur chantier | Arc électrode enrobée à l’atelier. |
Attention, pour certaines applications (tuyauterie sous pression, gaz, pétrole… ) les procédés peuvent être imposés par le bureau d’études ou donneur d’ordre.
Domaines d’utilisations (Qualité, coût, délais)⚓
A noter, que pour le domaine de l’agroalimentaire (fabrication de pate à tartiner par exemple) les soudures doivent être irréprochable, c’est-à-dire qu’elles ne doivent pas présenter de défaut et de cavité pouvant permettre la prolifération de bactéries.
Photo de soudure TIG | Photo avec inclusion ou défaut |
De nos jours, avec l’expansion de l’utilisation de la robotique, les entreprises investissent dans de nouvelles techniques de soudage lorsqu’elles ont des petites, moyenne ou grande série à fabriquer.
Exemple : le robot de soudage par apprentissage. |
L’opérateur, après avoir réalisé un montage d’assemblage, réalise une première soudure de l’ensemble. C’est alors que le robot enregistre les paramètres de déplacement (distance, vitesse, trajectoire) pour réaliser, par la suite la même soudure sur les autres pièces de la série.
Le coût de production est évidement réduit car :
Les pièces sont toutes réalisées de manière identique après validation d’une pièce test.
L’opérateur peut être différent car il suffit de charger / décharger les pièces soudées.
S33-2 Procédé soudage à l'arc avec électrode enrobée (111)⚓
Présentation
Procédé de soudage par fusion d'une électrode, due à la formation d'un arc électrique entre la pièce et cette électrode . La température de l'arc (environ 1500° C) porte instantanément l'électrode et le métal en fusion.
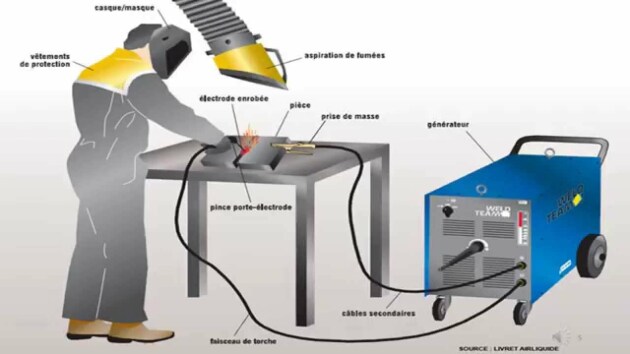
A compléter
Les paramètres définis⚓
Les paramètres définis : produits d'apports, type et Ø électrode, polarité, Uo.
Les paramètres variables⚓
Les paramètres variables : intensité, tension U1, vitesse d'avance, amorçage.
Complément : Présentation du procédé
S33-3 Procédés TIG (141)⚓
I : Le Procédé TIG, simple, efficace, et esthétique
Le Procédé TIG (acronyme de Tungsten Inert Gas) est un procédé de soudage électrique.
Très répandu dans l'industrie, ses applications sont nombreuses :
- agroalimentaire,
- pharmaceutique
- aéronautique
- tôlerie Fine
Il permet d'assembler de nombreuses nuances de métal (Aluminium, acier, inox)
II : Signification : Que veut dire TIG ?
Le "TIG" est un procédé de soudage 'n° 141. Son abréviation signifie:
- Tungsten
- Inert
- Gas
Cela signifie que pour ce procédé, il est utilisé une électrode réfractaire en Tungstène et qu'il y a un gaz inerte de protection du bain de soudage.
Les différents gaz sont : l'hélium, l'argon ou le mélange des deux.
III : Le fonctionnement d'un poste TIG
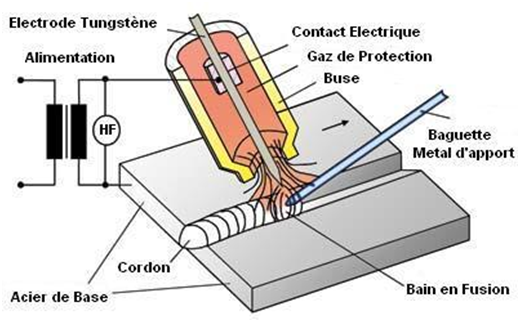
C'est un procédé de soudage à l'arc (141) dans lequel l'arc éclate au sein d'une atmosphère neutre (argon ou hélium) entre la pièce à souder et une électrode réfractaire (tungstène pur ou lanthane). Le procédé TIG permet le soudage des aciers inoxydables, de l'aluminium, du cuivre, du titane et de leurs alliages, etc... sur des épaisseurs comprises généralement entre 0.5 et 8 mm d'épaisseur.
Utilisé souvent en "première passe" pour les fabrications de hautes qualités. En effet, il permet une fusion parfaite des 2 métaux de base.
Souvent utilisé en automatique du fait des réglages simples
Courant continu pour le soudage des métaux "lourds" (ex : inox, aciers, etc.)
Courant alternatif pour le soudage des métaux "légers" (ex : aluminium).
IV : Le poste
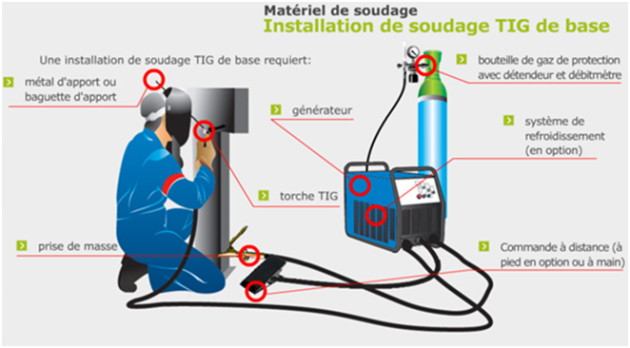
Sur certains poste, un refroidissement liquide peut être présent.
V : Composition de la Torche
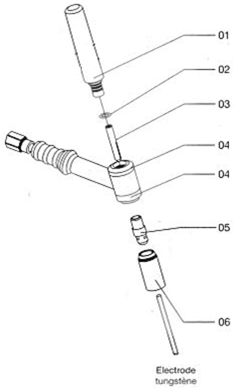
01 Bouchon
02 Joint de bouchon
03 Pince porte tungstène
04 Bague d'étanchéité / isolante
05 Siège
06 Buse
VI : Le refroidissement
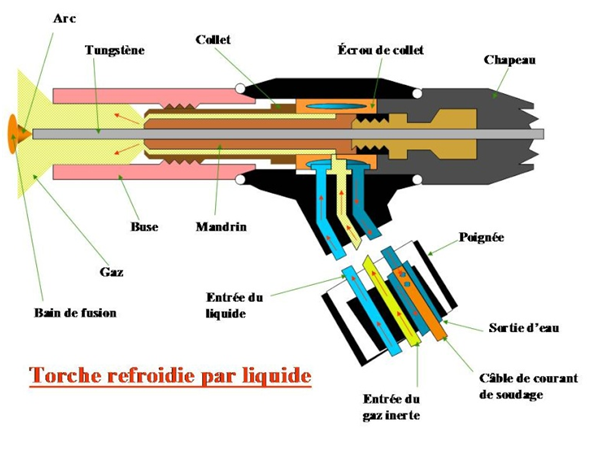
Le groupe de refroidissement par eau ou liquide de refroidissement est un dispositif utilisé pour le refroidissement de la torche lorsque cette dernière.
Utilisé pour éviter toute surchauffe en cas de soudage élevés. Cet appareil permet, au moyen d'une pompe, une circulation constante de liquide de refroidissement dans la torche et, au moyen d'un système de refroidissement, le contrôle des sur températures.
VII : Les gaz utilisés
Les deux principaux gaz utilisés en soudage TIG sont l'argon et l'hélium.
Ce sont deux gaz inertes, ce qui veut dire qu'ils protègent uniquement le bain de fusion. D'autres gaz inertes ont été essayés, mais leur faible production actuelle entraîne des pris élevés (Krypton, Xénon).
a. Argon :
Ce gaz se trouve dans l'atmosphère dans la proportion (non négligeable) de 0,94%. Il est un des produits de la distillation fractionnée de l'air liquide. On l'utilise en soudage sous diverses formes.
L'argon à 99,96% de pureté exprimée en VPM (ou parties en volume par million ou encore en cm3 par m3), ses impuretés ne dépassent pas : 100 VPM pour N2 50 VPM pour O2 et 300 VPM pour H2O.
L'argon raffiné à 99,995% pour les travaux de très hautes qualité. Les teneurs limites en impuretés sont 5 VPM pour O2 et H2O.
Un argon de moindre pureté que les précédents est utilisé en mélange avec CO2 et O2 et donne sur acier à bas carbone des soudures de meilleur aspect que le mélange gazeux réalisé avec l'argon - soudage dans la même proportion.
b. Hélium :
Pendant de nombreuses années, l'hélium était uniquement extrait des puits de gaz naturel d'Amérique du nord où on le trouve dans une proportion qui peut atteindre 2%. Considéré comme produit stratégique, l'importation de ce gaz en Europe est très limitée. Actuellement, on commence à extraire en quantité notable des gaz naturels européens, de sorte que son usage se développe.
L'hélium des soudeurs est à 99,995% de pureté. Les teneurs limites en impureté sont : h2 ≤ 5 VPM - O2 ≤ 5PM.
Pour le soudage, on utilise l'argon, l'hélium, le mélange de ces deux gaz, on peut aussi additionner un peut d'oxygène ou d'hydrogène pour le soudage des aciers inoxydables en automatique (vitesse élevée, pénétration importante).
Pour le soudage du Titane, du Tantale, du Zirconium, et tous métaux altérés à chaud par les gaz de l'atmosphère, on utilise de préférence de l'argon U. On additionne à la torche un système de protection supplémentaire, un traînard débitant de l'argon où le soudage s'effectue dans une "boîte à gant", sous atmosphère inerte.
VIII : Le Tungstène
La présence du thorium augmente le pouvoir émissif du tungstène, et permet une densité de courant plus élevée.
Il faut toujours utiliser une électrode de tungstène dans la fourchette supérieure de son intensité admissible.
Exemple : Pour souder à environ 110 A, en courant continu avec électrode en tungstène thorié, on choisira une diamètre de 1,6 mm au lieu d'un Ø de 2 mm.
On obtient une bonne stabilité de l'arc.
Le bon affûtage d'une électrode de tungstène est primordial pour assurer une bonne qualité de soudage. L'électrode fonctionne seulement comme support de l'arc, et par conséquent, ne doit pas fondre.
Le point de fusion de l'électrode de tungstène est de 3370°C.
Lorsqu'on soude au courant alternatif , il est nécessaire de fabriquer au bout de l'électrode une petite boule. (voir figure ci-dessous électrode de droite). Pour ce faire, il suffit d'amorcer l'électrode pour un moment sur une pièce de cuivre avec le courant continu à polarité inversée. Avec un tungstène au zirconium, la boule se fait automatiquement en courant alternatif avec haute fréquence continue.
Pour souder au courant continu, il suffit de meuler l'électrode comme l'indiquent les figures ci dessus. L'électrode en CCPI n'a pas besoins d'être préparé car à cette polarité la chaleur est concentré à environ 70% sur l'électrode qui aura tendance à fondre. Prévoir de baisser les paramètres avant de faire une hémisphère à l'extrémité du tungstène. D'ailleurs la polarité inversée est très rarement utilisée.
Affûtage en pointe pour le soudage des aciers courants en CC courant continu
Complément : Cours sur le soudage TIG
Rendez vous sur le site ROCDACIER pour un cours sur les paramètres de soudage TIG
Complément : Présentation du poste TIG
Complément : Notice du poste à souder
Un doute sur l'utilisation du poste à souder ?
Retrouver la notice d'un poste à souder présent dans notre atelier. Il permet de nombreux paramètres pour une soudure parfaite.
Rappel : Les Équipements de Protection Individuels
Comme pour tous les procédés, le gant de soudage est indispensable.
Il doit être fin et permettre à l'utilisateur d'appuyer sur la gâchette facilement.
Ci après une photo :
Aussi, vous aurez besoin du casque de protection à obscurcissement électronique (de préférence)
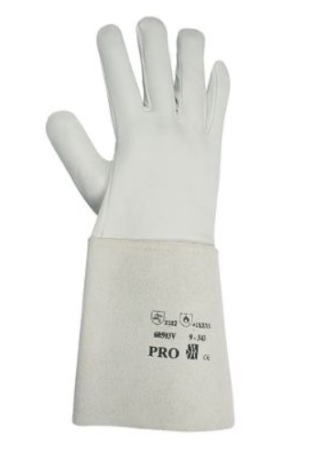
S33-4 Procédés semi automatiques (131, 135, 136, 138)⚓
I : Les Procédés MIG/MAG, fil fourré et simples, efficace
Les Procédés MIG / MAG sont des procédés de soudage électrique les plus répandus.
Très répandus dans l'industrie, ses applications sont nombreuses :
- construction métallique,
- chaudronnerie,
- tuyauterie
Il existe également d'autres procédé comme le Soudage semi automatique avec ou gaz avec fil fourré.
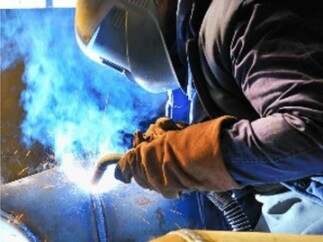
Voici précisément la nomenclature et numérotation des procédés de soudage :
131= Soudage MIG avec fil électrode fusible sous gaz inerte (GMAW)
135= Soudage MAG avec fil électrode fusible sous gaz actif (GMAW)
136= Soudage MAG avec fil fourré de flux sous gaz actif (FCAW)
138= Soudage MAG avec fil fourré de poudre métallique sous gaz actif (FCAW)
II : Signification : Que veut dire MIG / MAG ?
Le "MIG" est un procédé de soudage 'n° 131. Son abréviation signifie:
- Metal
- Inert
- Gas
Le MAG est similaire dans le fonctionnement, hormis le gaz et le fil utilisé. Le procédé de soudage est le n° 135. Son abréviation signifie:
- Metal
- Actif
- Gas
III : Le fonctionnement d'un poste MIG / MAG
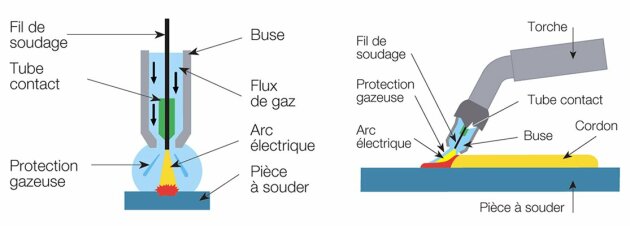
C'est un procédé de soudage à l'arc (131 ou 135) dans lequel l'arc éclate au sein d'une atmosphère gazeuse entre la pièce à souder et un fil d'acier.
IV : Le poste
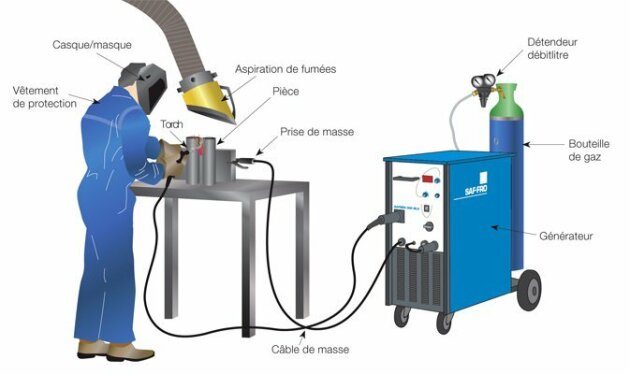
Complément : Cours sur le soudage MIG / MAG
Rendez vous sur le site ROCDACIER pour un cours sur les soudages MIG / MAG
Complément : Présentation du procédé MIG / MAG - no Gaz
Rappel : Les Équipements de Protection Individuels
Comme pour tous les procédés, le gant de soudage est indispensable.
Aussi, vous aurez besoin du casque de protection à obscurcissement électronique (de préférence)
Sans oubliés les équipement personnel et collectif :
S33-9 Procédés de soudage par résistance⚓
Le Soudage Électrique Résistance Par Point (SERP)
Le procédé Soudage Électrique Résistance par Point SERP est très utilisé dans le cadre de soudage de tôlerie fine. Il permet un assemblage rapide et efficace, sans déformation de la tôlerie.
Principe et matériel⚓
Explications
Les pièces à souder sont superposées et sont serrées localement entre deux électrodes en alliage de cuivre.
L'ensemble pièces / électrodes est traversé par un courant de soudage (de forte intensité et de basse tension) qui provoque une élévation de température et la fusion localisée des deux pièces dans la zone de positionnement des deux électrodes.
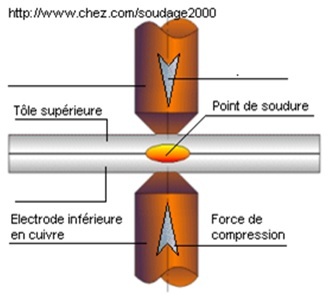
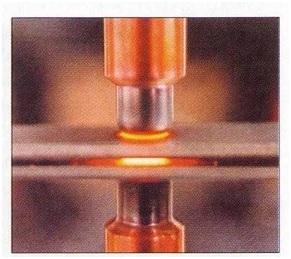
Soudage par point, à la molette.⚓
Soudage par point
LE soudage par point permet le soudage localisé des matériaux. Pour limiter les coût de fabrication, un écart entre deux point est calculé, ou défini. Un Positionnement par l'opérateur ou une centrale de soudage robotisée permet le soudage des pièces.
Le soudage par point ne permet pas l'étanchéité de la pièce car une distance entre 2 points de soudage existe.
Photo d'une pièce soudée par Points :
Contraintes constructives.⚓
Machine de soudage
Cycle de soudage - Les réglages⚓
Différentes phases
Evidement, pour chacun des procédés, des paramètres à régler existent. Cela est propre à chaque machine, Les capacités de soudage étant différentes entre les machines.
Le cycle de soudage est le suivant :
Accostage : Maintenir un bon contact entre les pièces à assembler.
Soudage : Le courant passe pendant un temps déterminé.
Forgeage ou maintien : Après soudage, les pièces sont maintenues pendant la solidification du point.
Temps de repos : C’est l’intervalle de temps entre 2 cycles consécutifs.
Avantages et inconvénients du procédé⚓
Les avantages
Rapidité d’exécution
Peu de déformations
Absence de préparation des bords à souder
Possibilité d’automatisation
Les inconvénients
Assemblage uniquement par recouvrement
Epaisseur soudée limitée à la puissance de la machine
Préparation des pièces⚓
Précaution à prendre avant soudage
Pour obtenir un soudage correct, il faut que les pièces soient exemptes :
de rouille
de calamine
de peinture
Les tôles abîmées doivent être décapées ou meulées.
La graisse et l’huile ne gène pas, mais la calamine lors du soudage provoque des étincelles.
Les revêtements électrolytiques (tôle électrozinguée) ne nuisent pas à la soudure.
Démarche de réglage du poste⚓
Les réglages spécifiques pour chaque poste à souder
Avant de valider les réglages, voilà les précautions à prendre :
Faire un essai au préalable sur des chutes de tôles de même nature et de même épaisseurs.
Contrôler l’assemblage : Un point doit se déboutonner et non se casser
Modification si besoin des paramètres : Temps de soudage et Intensité
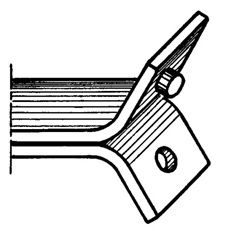
S34 – Les assemblages mécaniques⚓
S35 – Les procédés de manutention⚓
S4 : Qualité et contrôle⚓
S5 : La maintenance⚓
S6 : La santé, la sécurité au travail et la protection de l'environnement⚓
S61 – La prévention des risques, la santé et la sécurité⚓
Dans un atelier de chaudronnerie ou sur site d'interventions, les risques d'accidents sont possibles. La prévention est obligatoire pour éviter les accidents.
Comment travailler dans de bonnes conditions... ?
S61-1. La prévention des risques professionnels⚓
Pour prévenir les risques, pensons à l'affichage réglementaire...
S61-2. Les risques liés aux activités⚓
Protégeons nous ! ! les yeux, les oreilles, ... tous les membres (doigts, pied... )
S61-3. La typologie des lieux d'interventions⚓
Sur site, attention aux accès : l'échelle, l'escabaut...
S62 – Le développement durable et la protection de l'environnement⚓
Les déchets produits dans le cadre de l'activité industrielle de chaudronnerie doivent être évacués et éventuellement, recyclés.
Comment faire pour préserver l'environnement et rentrer dans une démarche de développement durable ?
S62-1. Le développement durable, l'économie circulaire et concepts de transition⚓
..
S62-2. La protection de l'environnement⚓
...
S62-3. L'identification, le stockage, l'évacuation des déchets liés à l'activité professionnelle⚓
...